1.Out fin and inner grooved tube machine
Straight out fin and inner grooved tube machine is used to produce the out fin and inner grooved tube, it is with the character of low investment and easy operation.
1.1. Technical parameter
1.1. Main motor: Main motor: 7.5kW 1440rpm.
1.2. Producing speed: 0.80~1.20meter/min (the speed is different according to different tube specification)
1.3. Tube to be produced: 12.7mm~25.4mm
1.4. Fin numbers (each inch): 19~60fins (for stainless steel tube max fin number is 40fins)
1.5. Fin height: 0.7mm~1.6mm (copper tube)
1.6. Inner groove number: 8~70teeth(70teeth only for copper tube)
1.7. Tube length: 300mm~6000mm
1.8. Tube material: Copper, aluminum, copper nickel, brass, carbon steel and stainless steel tubes
1.9. Compressed air pressure: 0.4-0.8Mpa 0.2m3/h
1.10. Machine overall dimension: 13500mm x 1350mm x 1150m Length x Width x Height
1.11. Electricity power: 380V 50HZ 3phases
1.2 Machine configuration and characteristic
The out-fin tube machine is composed of following structure: tube storage table, fin tube main machine, tube input and output frame system, mandrel table, hydraulic station, electrical control cabinet and accessories.
1.2.1. The tube storage table is used to load the raw material tube which is going to be produced, and its material is stainless steel with polished surface in case of tube surface of scratch. The tube storage table dimension is 6000x500mm.
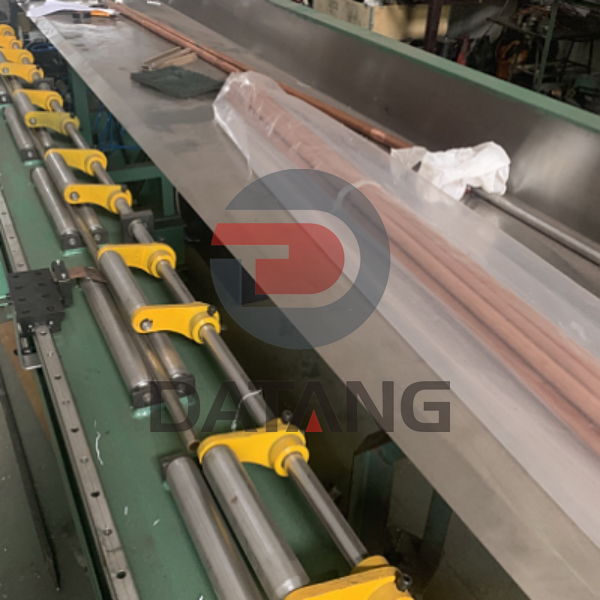